Advancing with Purpose: Automation at MCI Qingdao
Quality is essential to delivering on our commitments to sustainability, energy efficiency, and product reliability. This perspective guides ongoing investments in automation at our production site in Qingdao, where we are continuously adapting to evolving customer needs and regulatory requirements. Over the past year, targeted improvements have supported more consistent production outcomes, stronger traceability, and reduced environmental impact – contributing to a more resilient and efficient operation.
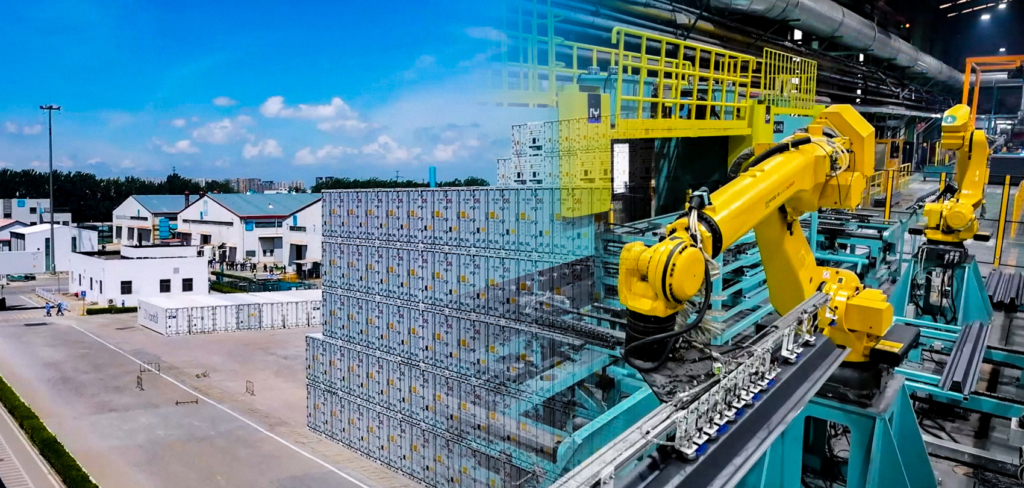
Enhancing Efficiency Through Automation
MCI’s automation efforts focus on building quality and consistency into the production of our Star Cool reefer units. Selected technologies – such as induction brazing for durable cooling circuit connections, automated tube bending for precise component shaping, and torque-monitored screwdrivers for consistent assembly – help reduce variation and support long-term performance. Enhanced scanning systems also improve component traceability throughout the production line, aiding serviceability over the product lifecycle.
These initiatives are part of our broader approach to manufacturing – prioritizing process control, product reliability, and environmental responsibility.
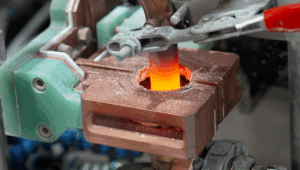
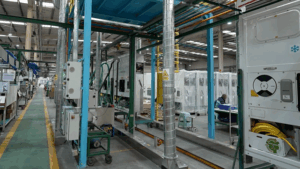
Preparing for the Next Generation of Refrigerants
In line with tightening environmental regulations, MCI Qingdao has implemented a flexible refrigerant charging system that now includes support for R1234yf. This low-GWP refrigerant, introduced with our Star Cool 1.1 units in 2024, is now charged in our reefers at the factory. This enables customers to reduce greenhouse gas emissions by up to one ton of CO₂-equivalent per unit annually. Additionally, it ensures seamless compatibility with our broader triple refrigerant platform, allowing the system to work efficiently with other refrigerants.
Extending Protection with Surface Treatment Enhancements
These automation initiatives build on earlier upgrades to surface treatment and zinc metallizing, introduced in Qingdao in 2023. Our process begins with robotized shotblasting for consistent surface preparation, followed by automated hot zinc metallizing for enhanced corrosion resistance. This method is both environmentally friendly and energy-efficient, with no chemical waste or VOC emissions. Final protective coatings are applied using semi-automated systems to ensure quality and durability.
Together, these upgrades support MCI’s goal of delivering long-lasting, high-performance equipment designed to perform reliably in demanding conditions.